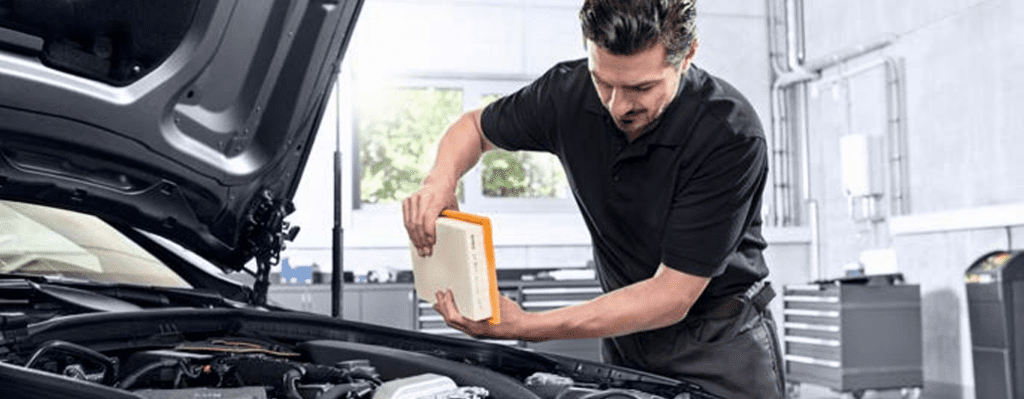
Engine technology has advanced at a significant rate over the last few years and with the development of long life oils, filter technology has had to move in line, so while the filter looks the same, its construction and installation has changed.
Knecht shares its advice to ensure correct fitment of its filters, first time, every time, as well as providing insight into this new technology and how the industry can best work with it.
HYDRAULIC FILTERS
Knecht is seeing more vehicles with special gear boxes and has developed its offering to provide workshop solutions with the correct equipment to drain the system and refill. Technicians shouldn’t assume it has been allowed to drain and that all the oil from the system has been removed.
Under or overfilling the gear box can cause damage here – and cost a lot to replace. Draining the system without the machine will only remove up to 50 percent of the oil from the system, against 90 percent using the correct machine.
OX FILTERS WITH FLEECE END CAP
When assembling Knecht oil filter inserts with the OX sales identifier, a bit more effort is required. There is a simple, practical reason for this.
To ensure a perfect seal between the clean and dirty sides of the oil circuit, the perforation in the fleece end cap developed by Knecht is slightly smaller than the corresponding counterpart in the housing cover. The fleece end cap is thus pressed in between the inner tube (filter) and the standpipe (cover), thereby acting as a “chambered seal”.
To decrease the slightly greater effort required, the fleece can be wetted with fresh engine oil prior to assembly.
FUEL FILTER ELEMENTS WITH MELTBLOWN COATING
In some Knecht fuel filter elements (KX), the surface appears to have a somewhat coarser fibre structure than normal, but exactly the opposite is true: these are highly efficient microfibres, applied to the filter paper as an extra layer during the melt-blown process.
The melt-blown coating is applied only to the inflow side (raw or dirty side) of the filter, allowing optimal filtering of the fuel, which flows from the outside toward the inside. The extremely fine melt-blown fibres with a diameter of less than 10 μm retain dirt and foreign particles even more effectively, while also increasing the service life of the filter.
With or without melt-blown fibres, cleanliness is a crucial consideration when replacing the fuel filter, as unpurified fuel must never get into the clean side of the filter, and therefore into the fuel injection system.
To minimise this risk, the remaining fuel should be drained out of the filter housing prior to assembly and disposed of in an environmentally friendly manner. Depending on the type, the filter should also be secured in the housing cover before insertion.
It is important that when replacing the fuel filter, all gaskets need to be coated with clean fuel prior to assembly in order to prevent damage during installation.
Once the filter has been replaced, the fuel system should be bled thoroughly. The key is to always follow the relevant manufacturer specifications.
LEAKY OIL FILTERS
In vehicles with spin-on (OC) oil filters, leakage from the filter or oil loss from the filter’s screw-on flange may occur due to a clogged control valve in the oil pump. This is visually confirmed when the seal has become dislodged or the filter housing has expanded, or even burst in some cases.
This can be typically attributed to deposits and carbonised residue in the engine oil that are swept through the oil pump, where they cause sporadic clogging of the control valve.
Since the oil pressure is no longer adequately regulated or may even cease to be regulated altogether, extreme pressure peaks of over 30 bar may occur as a result. The oil filter is unable to compensate for this tremendous rise in pressure and deforms.
BURST OIL FILTERS
The seal may become dislodged, or the end cap may bulge significantly, giving rise to insufficient contact pressure between the seal and the filter. As a result, oil is lost directly from the screw-on flange or the filter bursts – in which case the entire end cap detaches from the housing.
In the damage scenario described above, it is not enough to replace the filter. The technician should make absolutely certain that they inspect and flush the entire oil circuit to remove all deposits. They may also need to replace the oil pump (with integrated regulating valve).
Please click here to view the full range of KNECHT Filters stocked by APD Car Parts